Auto profi
Od simulace ozubeného kola po elektromotor. V Plzni vyvíjí a testují součástky aut pro celý svět
Navštívili jsme centrum ZF Engineering, kde se starají o to, aby každý díl nového vozu fungoval
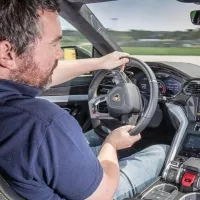
09.02.2023 10:18
0
Zdroj: Markéta Svatková, tiskový servis ZF
Sedíme na zadním sedadle moderního britského off-roadu Ineos Grenadier, který se pomalu pohybuje po ploše parkoviště. Náhle řidič z ničeho nic otevře dveře a pokusí se za jízdy vyskočit. Automatická převodovka ale okamžitě řadí polohu P a auto se s trhnutím zastavuje. „Vidíte,“ směje se zpoza volantu Jan Blahník, vedoucí týmu vývojových inženýrů pro diagnostiku, „to je jedna z těch situací, při které je potřeba myslet na bezpečnost. Aby auto samo nepokračovalo v jízdě a zastavilo. Tedy pokud nejede moc rychle,“ popisuje. Takových situací musí testeři z plzeňského ZF Engineering vyzkoušet mnoho, ať už v realitě nebo předtím v simulaci. Autosalon se byl v Plzni podívat, proč právě tahle česká pobočka patří k těm nejdůležitějším v portfoliu nadnárodního gigantu ZF.
Návštěva u "simulantů"
ZF má po Česku řadu továren, produkuje třeba brzdy v Jablonci nebo bezpečnostní pásy ve Staré Boleslavi. Plzeň je ale pro něj vývojovým hubem, sídlí tu pobočky ZF Openmatics zabývající se vývojem telematických systémů a produktové řady ZF Bus Connect, která se už podle názvu zabývá autobusy. Takovou vlajkovou lodí je tu ale vývojové centrum ZF Engineering, které má široký záběr od simulací až po reálné testování.
Abychom si celé centrum prošli takříkajíc od píky, začínáme právě u simulací. „Můžeme simulovat akustiku, vibrace nebo třeba proudění. Moje oddělení se konkrétně zabývá pevnostními výpočty a životností,“ vítá nás u takzvaných „simulantů“ Karel Dráždil. Ten se přímo specializuje na komplexní modely a u ZF v Plzni je už šest let. Přišel hned po škole. Právě oddělení, ve kterém vývojový inženýr působí, získalo zodpovědnost za výpočty životnosti a pevnostní výpočty pro další skupiny v rámci celé skupiny ZF. To jasně ukazuje, jak je plzeňské centrum pro ZF důležité.
„Naší misí je podpora vývoje systémů, kdy také zodpovídáme za virtuální validaci. Pomáháme kolegům i při vlastní výrobě, kdy s nimi řešíme konkrétní problémy. Jednoduše řečeno, udáváme směr vývoje, protože bez našeho oddělení si jen tak něco nevyzkoušíte,“ směje se s jistou dávkou hrdosti mladý inženýr.
A sám už své projekty potkává i v reálném provozu. Pracoval například na vývoji předního a zadního elektrického pohonu pro dva luxusní elektromobily, které jsou už dnes v prodeji. „Pracoval jsem na tom od samého začátku, tedy od prvních nákresů až po produkční linku. Takový projekt ale nikdy není one man show, byla potřeba globální spolupráce mezinárodního týmu. Dneska nás někdy ve firmě dávají za vzor,“ dodává Dráždil.
Ještě před pár lety byla simulace okrajovou záležitostí, komponenty se testovaly primárně fyzicky, bylo je tedy třeba vyrobit a pak zničit. Dnes je to přesně obráceně, protože na počítači se dají vyzkoušet tisíce scénářů, objekt se může jakkoliv namáhat a nekonečněkrát rozbít. Mnohdy k tomu stačí přitom práce jednoho inženýra. Simulace je tedy nejen výrazně efektivnější, ale také levnější.
Dráždil umí u každého komponentu spočítat i životnost. „Sice vám neřeknu, že třeba tahle věc vydrží přesně dva roky a jeden den,“ směje se s odkazem na tradiční vtip o zboží, které se rádo zkazí po uplynutí záruky, „ale dokážu vám říci, kolik cyklů vydrží. Pak už je práce technika, který ví, jak se bude daný komponent chovat, a podle toho zjistí životnost,“ dodává. Ale příklad přece jen nakonec má: „V Číně je město Harbin, kde jsou extrémní výkyvy teplot, tedy v létě je tam vedro a v zimě tuhý mráz. Tam by měly ty nejvíc namáhané součásti elektromotorů vydržet v provozu minimálně deset let.“
Mimochodem, Dráždilovou specialitou je korekce ozubení. V elektromobilech jde o tichý provoz a někdy se může stát, že je systém prostě příliš hlučný. „My jsme schopni ho zkoumat a následně optimalizovat. Odvalování ozubení je dynamický jev, který jsme schopni lidově řečeno rozsekat na malé časové kousky a podívat se na to, v jakých pozicích je nejvíc namáháno. Tam pak hledáme hluk,“ popisuje. To už ho ale kolegové upozorňují, že zachází snad až příliš do detailů.
Abychom si celé centrum prošli takříkajíc od píky, začínáme právě u simulací. „Můžeme simulovat akustiku, vibrace nebo třeba proudění. Moje oddělení se konkrétně zabývá pevnostními výpočty a životností,“ vítá nás u takzvaných „simulantů“ Karel Dráždil. Ten se přímo specializuje na komplexní modely a u ZF v Plzni je už šest let. Přišel hned po škole. Právě oddělení, ve kterém vývojový inženýr působí, získalo zodpovědnost za výpočty životnosti a pevnostní výpočty pro další skupiny v rámci celé skupiny ZF. To jasně ukazuje, jak je plzeňské centrum pro ZF důležité.
„Naší misí je podpora vývoje systémů, kdy také zodpovídáme za virtuální validaci. Pomáháme kolegům i při vlastní výrobě, kdy s nimi řešíme konkrétní problémy. Jednoduše řečeno, udáváme směr vývoje, protože bez našeho oddělení si jen tak něco nevyzkoušíte,“ směje se s jistou dávkou hrdosti mladý inženýr.
A sám už své projekty potkává i v reálném provozu. Pracoval například na vývoji předního a zadního elektrického pohonu pro dva luxusní elektromobily, které jsou už dnes v prodeji. „Pracoval jsem na tom od samého začátku, tedy od prvních nákresů až po produkční linku. Takový projekt ale nikdy není one man show, byla potřeba globální spolupráce mezinárodního týmu. Dneska nás někdy ve firmě dávají za vzor,“ dodává Dráždil.
Ještě před pár lety byla simulace okrajovou záležitostí, komponenty se testovaly primárně fyzicky, bylo je tedy třeba vyrobit a pak zničit. Dnes je to přesně obráceně, protože na počítači se dají vyzkoušet tisíce scénářů, objekt se může jakkoliv namáhat a nekonečněkrát rozbít. Mnohdy k tomu stačí přitom práce jednoho inženýra. Simulace je tedy nejen výrazně efektivnější, ale také levnější.
Dráždil umí u každého komponentu spočítat i životnost. „Sice vám neřeknu, že třeba tahle věc vydrží přesně dva roky a jeden den,“ směje se s odkazem na tradiční vtip o zboží, které se rádo zkazí po uplynutí záruky, „ale dokážu vám říci, kolik cyklů vydrží. Pak už je práce technika, který ví, jak se bude daný komponent chovat, a podle toho zjistí životnost,“ dodává. Ale příklad přece jen nakonec má: „V Číně je město Harbin, kde jsou extrémní výkyvy teplot, tedy v létě je tam vedro a v zimě tuhý mráz. Tam by měly ty nejvíc namáhané součásti elektromotorů vydržet v provozu minimálně deset let.“
Mimochodem, Dráždilovou specialitou je korekce ozubení. V elektromobilech jde o tichý provoz a někdy se může stát, že je systém prostě příliš hlučný. „My jsme schopni ho zkoumat a následně optimalizovat. Odvalování ozubení je dynamický jev, který jsme schopni lidově řečeno rozsekat na malé časové kousky a podívat se na to, v jakých pozicích je nejvíc namáháno. Tam pak hledáme hluk,“ popisuje. To už ho ale kolegové upozorňují, že zachází snad až příliš do detailů.
Vysoké napětí
I když je virtuální testování dnes už nepostradatelné, je přece jen vždy potřeba mít i fyzické objekty. Proto pokračujeme do laboratoří, kde pracují testeři a developeři. Vítá nás Karel Čermák, šéf hardwarového vývoje elektroniky pro zákazníky. Je tu celkem 12 pracovišť, některá jsou nízkonapěťová, jinde se se pracuje s vysokým napětím. Do něj se počítá už 60V. Nejvíce se pracuje se 400V systémy, ale umí tu i 1000 V. To se v době raketového tempa vývoje elektromobilů a plug-in hybridů hodí, protože už automobilky počítají i s 800V sítěmi. V budoucnu by mohly mít i 1200 V. To už bude ale potřeba laboratorní zařízení mírně upravit.
Pracovníci tady testují nejrůznější situace, do kterých se mohou komponenty s tištěnými spoji dostat. Dnes jde hlavně o řídící jednotky elektromotorů, proto se zkouší na různé zátěže a teploty. „Když selže jedna součástka, nesmí to zničit ostatní komponenty a nesmí to ohrozit bezpečnost v provozu. Proto vyvoláváme různé provokace. Jsme navíc schopni testovat komponenty v teplotách od minus 40 do plus 105 stupňů Celsia,“ říká Čermák.
V laboratoři pro test vysokého napětí je potřeba dodržovat zásady bezpečnosti. A tak zatímco u nízkého napětí se stačí zbavit statické elektřiny (třeba tím, že lidé nosí speciální obuv), tady je připravená průhledná komora, kam se komponenta zavře a testuje se pak vzdáleně. „Dokud se nezavřou dveře do komory, tak se test ani vysoké napětí nespustí. Stejně tak se zase neotevřou, dokud test neskončí. K dispozici je i připravený odpor, kam se přebytečná elektrická energie přesune, aby nikoho neohrozila,“ ukazuje nám laboratoř Čermák.
Pracovníci tady testují nejrůznější situace, do kterých se mohou komponenty s tištěnými spoji dostat. Dnes jde hlavně o řídící jednotky elektromotorů, proto se zkouší na různé zátěže a teploty. „Když selže jedna součástka, nesmí to zničit ostatní komponenty a nesmí to ohrozit bezpečnost v provozu. Proto vyvoláváme různé provokace. Jsme navíc schopni testovat komponenty v teplotách od minus 40 do plus 105 stupňů Celsia,“ říká Čermák.
V laboratoři pro test vysokého napětí je potřeba dodržovat zásady bezpečnosti. A tak zatímco u nízkého napětí se stačí zbavit statické elektřiny (třeba tím, že lidé nosí speciální obuv), tady je připravená průhledná komora, kam se komponenta zavře a testuje se pak vzdáleně. „Dokud se nezavřou dveře do komory, tak se test ani vysoké napětí nespustí. Stejně tak se zase neotevřou, dokud test neskončí. K dispozici je i připravený odpor, kam se přebytečná elektrická energie přesune, aby nikoho neohrozila,“ ukazuje nám laboratoř Čermák.
Zdroj: Markéta Svatková, tiskový servis ZF
Svezení s Ineosem
Aby byl vývojový řetěz kompletní, vycházíme na závěr naší prohlídky na parkoviště před ZF Engineering. Potkáváme tam právě Jana Blahníka a jeho kolegyni Andreu Lodrovou z diagnostického týmu. „My jsme už na té vrchní úrovni ve vývoji softwaru. Jsme v přímém kontaktu se zákazníkem a ladíme finální produkt přesně podle jeho potřeb. Případné problémy se snažíme vyřešit. Není to ale jen tak, máme třeba půl milionu řádků kódu,“ říká nám Andrea Lodrová, když usedáme na palubu Ineosu Grenadier. Její kolega řídí, ona má připojený počítač a v reálném čase tak může kontrolovat to, co řidič nemůže vidět – chování řídící jednotky.
Auto, ve kterém jsme, slouží k testu chování převodovky. Vypadá v podstatě normálně. „To je ta situace, kdy máme sériově vyráběnou převodovku a tedy máme připojeno jen pár kabelů. Někdy máme ale externí aplikační jednotku. V tom případě se řídící jednotka nachází v interiéru vozidla pro snazší přístup k ní,“ vysvětluje Lodrová.
To už se ale její kolega rozjíždí, aby demonstroval některé funkce. Kromě ukázky automatického zařazení polohy P při pokusu opustit vozidlo, kontroluje třeba nastavení automatu pro režim průtahové mycí linky, kdy musí systém zůstat v poloze neutrálu, jinak by myčka auto vláčela se zaseknutými koly.
„Každý monitoring chyby v softwaru je potřeba vyladit tak, aby nedocházelo k nerelevantním výskytům chyby, které by nepotěšily jak zákazníka, tak ani automobilku. Pokud monitoring funguje správně, velice přesně pomůže lokalizovat chybu v systému, i mechanickou. Každé uložení chyby je zaznamenáno v paměti chyb, kterou všichni známe, pokud přistupujeme k OBD Diagnostickému konektoru. A však v případě OBD-II normy už nelze chybu napřímo smazat přes servisní požadavek, ale vozidlo musí absolvovat několik za sebou jdoucích jízdních cyklů bez chyb (laicky řečeno teplých jízd) pro její smazání,“ popisuje Blahník.
Neustálá kalibrace, monitoring funkcí a úprava kódu je pro inženýry z plzeňské společnosti denním chlebem. Samozřejmě nejezdí tady po parkovišti v Plzni, to teď slouží jen pro ukázku. S auty se vydají třeba na letiště nebo do testovacích center ZF. Řidiči ale míří i přímo k automobilkám. Každá značka má totiž na chování svých komponent jiné požadavky. Každopádně po návštěvě vývojového centra ZF Engineering v Plzni je jasné, že bez českých inženýrů se už dnešní automobilový svět jen tak neobejde.
Auto, ve kterém jsme, slouží k testu chování převodovky. Vypadá v podstatě normálně. „To je ta situace, kdy máme sériově vyráběnou převodovku a tedy máme připojeno jen pár kabelů. Někdy máme ale externí aplikační jednotku. V tom případě se řídící jednotka nachází v interiéru vozidla pro snazší přístup k ní,“ vysvětluje Lodrová.
To už se ale její kolega rozjíždí, aby demonstroval některé funkce. Kromě ukázky automatického zařazení polohy P při pokusu opustit vozidlo, kontroluje třeba nastavení automatu pro režim průtahové mycí linky, kdy musí systém zůstat v poloze neutrálu, jinak by myčka auto vláčela se zaseknutými koly.
„Každý monitoring chyby v softwaru je potřeba vyladit tak, aby nedocházelo k nerelevantním výskytům chyby, které by nepotěšily jak zákazníka, tak ani automobilku. Pokud monitoring funguje správně, velice přesně pomůže lokalizovat chybu v systému, i mechanickou. Každé uložení chyby je zaznamenáno v paměti chyb, kterou všichni známe, pokud přistupujeme k OBD Diagnostickému konektoru. A však v případě OBD-II normy už nelze chybu napřímo smazat přes servisní požadavek, ale vozidlo musí absolvovat několik za sebou jdoucích jízdních cyklů bez chyb (laicky řečeno teplých jízd) pro její smazání,“ popisuje Blahník.
Neustálá kalibrace, monitoring funkcí a úprava kódu je pro inženýry z plzeňské společnosti denním chlebem. Samozřejmě nejezdí tady po parkovišti v Plzni, to teď slouží jen pro ukázku. S auty se vydají třeba na letiště nebo do testovacích center ZF. Řidiči ale míří i přímo k automobilkám. Každá značka má totiž na chování svých komponent jiné požadavky. Každopádně po návštěvě vývojového centra ZF Engineering v Plzni je jasné, že bez českých inženýrů se už dnešní automobilový svět jen tak neobejde.
Diskuze
Žádné příspěvky, buďte první!
ZF představilo vyhřívané bezpečnostní pásy. Mají pomoci zvýšit dojezd elektromobilů
Vyhřívání spotřebuje mnohem méně elektrické energie než topení. A má být i příjemnější
05.01.2023 10:43
|
4
Flexibilní pracovní dobu a neustálý rozvoj. ZF se ptalo svých inženýrů, co potřebují k práci
Technologická firma má v Česku několik továren, i proto se ptala také tuzemských zaměstnanců
13.12.2022 16:56
|
1
Dřív tu vyráběli brzdy pro Favorit, teď pro Rolls-Royce. Navštívili jsme továrnu ZF v Jablonci
Ročně vyprodukují na devět milionů brzd, chtějí ale víc. Také je tu testují v extrémních podmínkách
30.09.2022 15:29
|
2
Policisté zažili honičku jako z akčního filmu. Zfetovaný řidič ujížděl i přes zastavovací pásy
Z auta muže donutily vystoupit až namířené policejní zbraně. Hrozí mu pár let ve vězení
15.11.2021 11:32
|
0
I majitelé benzinových aut by měli řešit zimní palivo. U dieselů zas hrozí zamrznutí AdBlue
Pokud tankujete do svého vozu jen občas, raději palivo před zimou vyjezděte. Vyhnete se potížím
19.11.2024 15:54
|
4
Tady je nebezpečné tankovat. ČOI rozdala čerpacím stanicím další pokuty za nekvalitní palivo
Desetitisícové pokuty od inspekce schytaly pumpy v Praze, Středočeském a Ústeckém kraji
19.11.2024 14:00
|
14
O rychlost nejde. V Praze je kamera, která kontroluje častý přestupek spěchajících řidičů
Kameru najdete v Evropské ulici. Autosalon zjišťoval, zda už rozesílá pokuty tak, jak se slibovalo
19.11.2024 09:57
|
6
Volkswagen Golf jako hybrid do zásuvky jezdí příjemně. Otázkou je, zda za něj dát přes milion
Ujede 100 km na jedno nabití, využije i rychlé nabíječky. Zkoušeli jsme, kolik spolyká bez elektřiny
19.11.2024 07:58
|
2